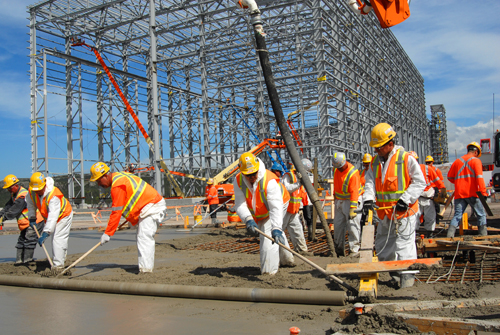
The Vale do Rio Doce in Brazil is doubtless an idyllic place beauty as its name, valley of the peaceful river, implies. However the now more prosaically named Vale is a global company with which readers of Business Excellence are very familiar, most recently in our coverage of Vale's coal mining operations in Mozambique – and indeed, Wales.
However since its 2006 acquisition of Canadian nickel mining operator Inco Vale has been a major player in Canada, where it now has a dozen mines and operational sites. To give an idea of the scale of the Canadian operations, now a wholly owned subsidiary of the Brazilian major, its base metals headquarters in Toronto alone employs 850 people at three sites that administer Vale's countrywide operations and house the company's technology development department. Base metals in this context covers almost everything apart from gold, silver and platinum, and definitely includes nickel.
Also in Ontario, though about 400 kilometres to the north of Toronto, Sudbury has enough untapped nickel deposits to support mining for decades to come. In total, Vale has six mines, a mill, a smelter and a refinery in Sudbury, making this one of the largest integrated mining operations on the planet, employing approximately 4,000 people. Raw materials from Vale’s Sudbury operations are shipped to The Port Colborne nickel refinery, a vast 360-acre complex on the shore of Lake Erie in southern Ontario. The refinery dates back to the early days of Inco nearly 100 years ago and employs 170 people in processing nickel, electrocobalt and precious metals, exporting finished nickel products throughout the world.
Over in northern Manitoba , the operation at Thompson (named after John F Thompson, chairman of International Nickel when a significant body of ore was discovered there in 1956) is located 740 kilometres north of Winnipeg and is known as Vale's northern hub. Operations, there consist of the Thompson and Birchtree Mines along with the Thompson mill, smelter and refinery, which between them employ about 1,500 people and cover some 250 acres.
From there we can proceed to an area where Vale is currently making major investments. St. John’s, the province’s capital city, is home to Vale's Newfoundland and Labrador corporate office from which its operations in Voisey’s Bay and Long Harbour are controlled. These two sites produce nickel and copper concentrates, employing 580 full-time staff supported by more than 3,000 contractors.
The main features of the Voisey’s Bay site, which is remote by any standards and during the winter very cold indeed, are the open pit, the concentrator, waste rock storage areas, sedimentation ponds and tailings disposal areas. The mine opened in 2005, and the site also includes vast deposits with potential for future underground operations. Vale has committed to developing deeper mining, creating hundreds of jobs. However most of the workers need to be brought in. They generally work on a two-week rotation at the fly in/fly out operation. While at site, workers live in an accommodation complex that contains cafeterias, recreational areas, shops, offices and medical facilities. To get the ore out, the company makes use of a purpose built polar-class ice breaking bulk carrier, the Umiak I. This is the world’s most powerful ice breaking cargo ship powered by a 30,000 horsepower engine, large enough to drive an oil tanker ten times as big. Making twelve trips a year, the ship brings supplies in, and carries up to 30,000 tonnes of nickel ore to Quebec City from where it is sent by rail to Vale’s Sudbury smelter.
That's for now. But Vale is building a major complex much nearer, on a partially brownfield site near the port of Long Harbour in Newfoundland and Labrador that will be fed from Voisey's Bay. Vale’s objective for the nickel processing plant is to process concentrate from the mine and concentrator in northern Labrador to produce finished nickel product and associated cobalt and copper products. The $4 billion plant includes concentrate offloading, crushing, and grinding facilities located near the wharf. The main processing plant is located approximately 2 kilometres south of the port facility and additionally there is a pipeline to supply process water, an effluent discharge pipe and diffuser into the harbour and a residue pipeline into a nearby disposal area. The plant site will house a complex process in which concentrate is pressure-levelled in acidic solutions to separate iron, sulphur, and other impurities from nickel, copper, and cobalt.
A joint venture of Alberici and Black and McDonald has erected 263,000 square foot steel building modules for the nickel/cobalt electrowinning building and the 182,000 square foot neutralization building at the new facility, and Fluor is performing engineering, procurement and construction management services . The plant, scheduled to start production in 2013 but delayed by labour problems, should be in operation this year. Vale is committed to providing a safe work environment for all employees and subcontractors. As part of that commitment, the companies involved produced a safety video to be shown to all employees working on the project.
As an operator in Canada, including some of its most environmentally sensitive areas of pristine wilderness, Vale is committed to the challenges of climate change. In 2008 it launched its Carbon Program, a set of global actions that promote the strategy of reducing greenhouse gas emissions by using new technologies and less carbon-intensive processes. Canada has benefited from this commitment with initiatives such as the Clean AER project, which will not only help the environment, but it will ÔÇïalso increase the quality of life in the city of Sudbury. With funding of US$ 1 billion, this is the largest single environmental investment in the history of Sudbury– and one of the largest in Ontario. The core of the project is an 85 percent reduction in sulphur dioxide emissions from Vale’s smelter in Sudbury, and a significant reduction in metals and particulate emissions. The project is expected to be complete in 2016.
Written by John O’Hanlon, research by Robert Hodgson